Covering Embodied Carbon Series
Covering Embodied Carbon: how do I measure it?
Read Time 6 mins | Written by: Alex Bantock
TL;DR
- The building lifecycle framework is made up of four lifecycle stages: product [A1-A3], construction [A4-A5], use [B1-B7], and end-of-life [C1-C4]
- The carbon footprint of a construction material/product is often reported by manufacturers, along with other environmental impacts, in Environmental Product Declarations (EPDs)
- It is recommended to use an LCA tool that can be used early in the building design phase, has transparent and quality data, allows for comparison of design iterations, and can be used for a Whole Life Carbon view of the building
We have seen how embodied carbon is a class of emissions that needs to be reduced within the built environment. But before we can talk about reducing it, we first need to understand how to measure it. If you recall in our previous posts, we described embodied carbon as the greenhouse gases (GHGs) emitted during the creation and disposal of construction materials.
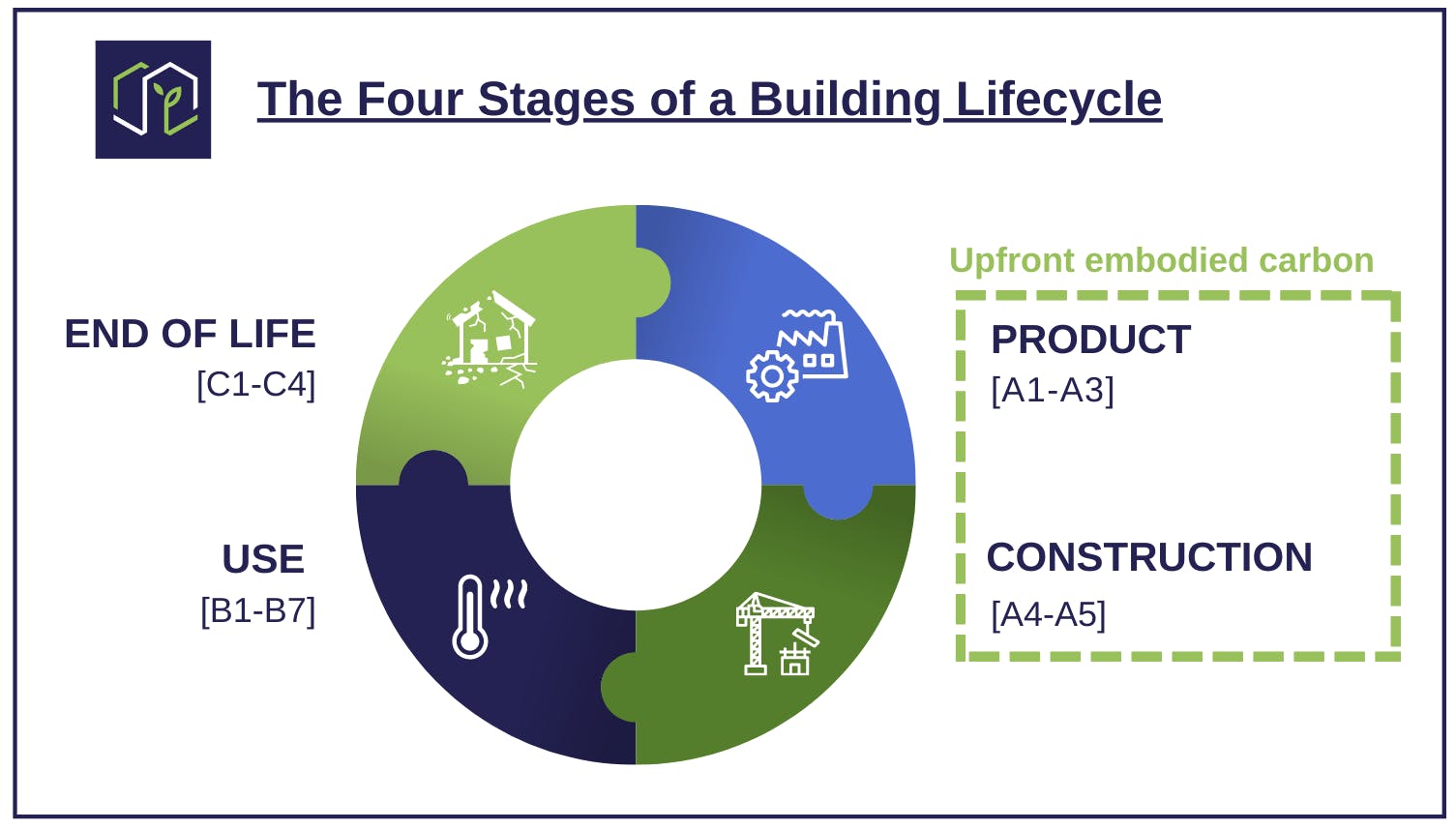
Life cycle stages and modules
As touched upon briefly, we use a lifecycle framework to measure embodied carbon, since different amounts of carbon are released during the different building lifecycle stages. The framework is comprised of four lifecycle stages, which are in turn made up of individual modules. Terms frequently used to encompass a set of lifecycle stages (called the scope) include “cradle to gate”, “cradle to practical handover”, and “cradle to grave”. For example, below we can see that the material extraction [A1], transport [A2], and manufacturing [A3] modules (or the Product stage [A1-A3]) are known as “cradle to gate” embodied carbon - i.e. from raw material extraction to the gate of the manufacturer. When the transport of the manufactured materials [A4] and construction and installation processes [A5] are included, it is known as “cradle to practical handover” - i.e. from raw material extraction to just before building occupation and use. And again, the inclusion of the Use stage [B1-B7] and End of Life stage [C1-C4] is called “cradle to grave” - i.e. from raw material extraction to material disposal.
Download our Building Life Cycle Diagrams here
To account for the GHG emissions emitted or sequestered during each life cycle stage, we perform what’s called a life cycle assessment (or LCA for short). So, let’s perform a simple life cycle assessment to measure the “cradle-to-gate” ([A1-A3]) embodied carbon of a steel beam. During the Extraction ([A1]) lifecycle stage, we would account for all of the GHGs emitted during the mining of the raw materials, such as iron ore. We would then account for the GHG emissions of transporting those raw materials ([A2] Transportation) to the manufacturing facility. At the facility, the fuels and electricity used by the furnace and mills would emit carbon, and we would total up those emissions as well. When all the processes required to turn the raw materials into a hot-rolled steel beam (the final product) are accounted for (this often includes multiple transportation and manufacturing steps that we’re now skipping for simplicity), we would total all those emissions to report the “cradle-to-gate” embodied carbon. This carbon footprint of a construction material/product is often reported by manufacturers, along with other environmental impacts, in Environmental Product Declarations (EPDs). EPDs are important as they are transparent and comparable documents that allow specifiers to make informed decisions.
At this point, we can continue accounting for the emissions throughout the construction process. From the “gate” of the manufacturer, materials are then transported to the construction site, and we capture these emissions for each material in the [A4] Transportation phase. Then, as on-site construction begins, we account for the GHG emissions needed to construct the building, for example, the electricity used for the cranes and the diesel used for equipment (the [A5] Construction phase). Together, these “cradle to practical handover” emissions ([A1-A5]) make up the ‘upfront’ embodied carbon of a building (or “embodied carbon to practical completion”).
See RICS Whole life carbon assessment for the built environment for a more in-depth explanation of each of the stages and their calculation methods.
It is important to note that life cycle assessments and transparency are critical for determining embodied carbon - do not be fooled by materials that look identical, have similar costs, and share the same performance characteristics, as they could (and probably do) have completely different embodied carbon values. For example, one lot of hot-rolled steel beams could be made from virgin steel using coal-fired furnaces and transported long distances, whereas the other could be 100% recycled steel from a local manufacturer using renewable energy. The same end product, completely different carbon impact!
Tools to measure embodied carbon
There are various LCA tools available for calculating the carbon footprint of a building or product. However, choosing the right tool is important, depending on what you wish to gain from your LCA. We recommend incorporating the following factors into your decision-making process when choosing an LCA tool, as a tool that satisfies these recommendations is more likely to achieve accurate results that are close to as-built values and allow for informed decisions:
i) The earlier a tool can perform an LCA in the building design phase, the better
ii) The underpinning data used in the analysis should be known and of quality
iii) One should be able to seamlessly compare alternative building designs, materials, and subsequent LCAs to determine the best solution
iv) A whole-life carbon view of the building is advised as it allows for ongoing monitoring and benchmarking throughout the building lifecycle
Whilst there are a number of solutions on the market that offer LCAs, it is currently a fragmented ecosystem of small tools that do not satisfy what is needed to make a meaningful difference in the carbon impact of a building. For example, tools are often used too late in design to make a meaningful difference, use a variety of datasets which make results incomparable, make it difficult and time-consuming to assess and compare multiple design iterations, and do not adopt a whole life carbon approach thus often covering only a portion of the building lifecycle.
Since consistency and transparency in reporting and harmonisation of calculations are soon to be mandated in the industry, there is a pressing need for a centralised commercial solution that can address all of the above factors. If you’d like to know how Preoptima can elegantly address all of these pain points for you - check out our blog post on how we save you time, money, and carbon; or contact us at info@preoptima.com.
We'd love to hear from you!